The operation of an industrial fluid system depends on the collaboration of each component that delivers your process fluid to its destination. The safety and productivity of your plant depend on leak free connections between components. To identify the fitting for your fluid system, first understand and identify the thread size and pitch.
Thread and termination Foundation
Even experienced professionals sometimes find it difficult to identify threads. It is important to understand general thread and termination terms and standards to help classify specific threads.
Thread type: external thread and internal thread refer to the position of thread on the joint. The external thread is protruding on the outside of the joint, while the internal thread is on the inside of the joint. The external thread is inserted into the internal thread.
Pitch: pitch is the distance between threads. Pitch identification depends on specific thread standards, such as NPT, ISO, BSPT, etc. Pitch can be expressed in threads per inch and mm.
Addendum and dedendum: there are peaks and valleys in the thread, which are called addendum and dedendum respectively. The flat surface between the tip and the root is called the flank.
Identify thread type
The first step to identify thread size and pitch is to have proper tools, including vernier caliper, pitch gauge and pitch identification guide. Use them to determine whether the thread is tapered or straight. tapered-thread-vs-straight-thread-diagram
Straight thread (also called parallel thread or mechanical thread) is not used for sealing, but is used to fix the nut on the casing connector body. They must rely on other factors to form leak proof seals, such as gaskets, O-rings, or metal to metal contact.
Tapered threads (also known as dynamic threads) can be sealed when the tooth sides of the external and internal threads are drawn together. It is necessary to use thread sealant or thread tape to fill the gap between tooth tip and tooth root to prevent leakage of system fluid at the joint.
The taper thread is at an angle to the center line, while the parallel thread is parallel to the center line. Use vernier caliper to measure the tip to tip diameter of external thread or internal thread on the first, fourth and last full thread. If the diameter increases on the male end or decreases on the female end, the thread is tapered. If all diameters are the same, the thread is straight.
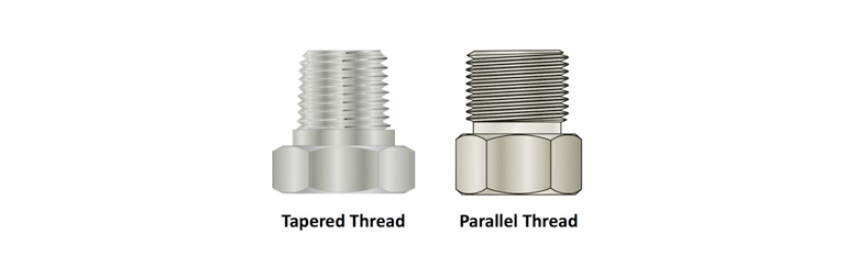
Measuring thread diameter
After you have identified whether you are using straight or tapered threads, the next step is to determine the diameter of the thread. Again, use vernier caliper to measure the nominal external thread or internal thread diameter from the top of the tooth to the top of the tooth. For straight threads, measure any full thread. For tapered threads, measure the fourth or fifth full thread.
The diameter measurements obtained may be different from the nominal sizes of the given threads listed. This change is due to unique industrial or manufacturing tolerances. Use the connector manufacturer's thread identification guide to determine that the diameter is as close to the correct size as possible. thread-pitch-gauge-measurement-diagram
Determine pitch
The next step is to determine the pitch. Check the thread against each shape with a pitch gauge (also known as the comb) until a perfect match is found. Some English and metric thread shapes are very similar, so it may take some time.
Establish pitch standard
The final step is to establish the pitch standard. After the sex, type, nominal diameter and pitch of thread are determined, the thread identification standard can be identified by thread identification guide.
Post time: Feb-23-2022