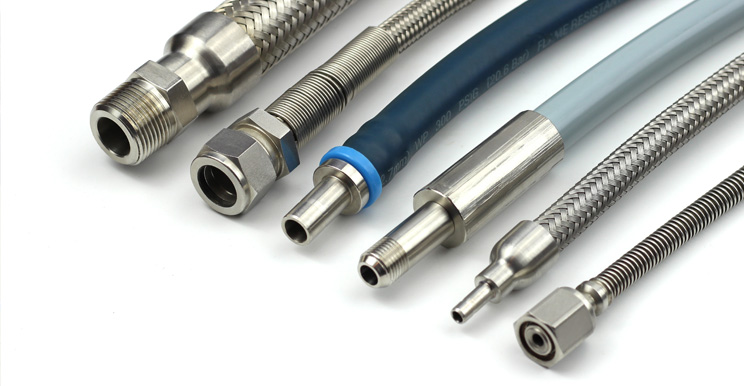
Industrial hose: It is mainly used for soft connection between various equipment. So, what can be done to extend its service life? A good maintenance plan for industrial hoses will save your factory a lot of money.
Steps to develop a preventive industrial hose maintenance plan:
1. Identify all hoses:
First, perform a complete factory audit, including identifying and marking each hose. The audit should be comprehensive and specific, including recording hose type, part number, process fluid, pressure or temperature ratings, and supplier name and contact information. In the spreadsheet, record other detailed information, including the length, size, inner material and structure of each hose, reinforcement, termination, installation environment, outer layer type, application environment, cleaning procedures, and hose installation and planning The date of replacement.
2. Track the life cycle of each hose:
Follow the regular hose inspection schedule and inspect each hose at the interval recommended by the supplier. Only a visual inspection is required, so system shutdowns are rarely required. You mainly check for signs of wear, such as scratches, cuts, corrosion, kinks and general degradation. These signs indicate that the hose should be replaced. Please note all observations in the spreadsheet.
After the hose has reached the end of its service life, be sure to pay attention to its maintenance interval. This information provides a definite replacement cycle for the hose.
If the hose fails during operation, please record every detail: the location of the failure on the hose, the severity of the break, and how the hose is installed. These details will help to troubleshoot with the hose supplier and determine how to prevent accidents from happening again.
3. Reduce hose stress:
If the system is running at the time of the inspection, determine any known conditions created by the hose. Inspect hoses installed in arrangements that rub against equipment, are subjected to vibration, are exposed to external heat sources, or are installed in arrangements that may cause excessive strain. The above situation should be corrected immediately, otherwise it will shorten the service life of the hose or cause a malfunction. The following are common causes of hose strain:
(1) Twist the hose or bend it on multiple planes
(2) Bend the hose beyond the recommended radius
(3) Bend too close to the hose/connector connection
(4) Use a hose with insufficient length, so the hose will be stressed during the impact
(5) No elbows and adapters are used to relieve hose stress at the horizontal end connection
4. Determine whether you need to protect the outer layer:
When choosing the protective outer layer, you must carefully understand the operating temperature of each option and the main purpose of its function. For example, thermowells can protect hoses from splashes of molten weld metal, but they cannot prevent wear.
5. Follow the inspection and replacement protocol
After you understand the replacement interval of each hose, your hose maintenance plan will take shape. However, even after determining the replacement interval, you should continue to check regularly to ensure that changes in system parameters will not cause strain on the hose.
6. Analyze the data
Periodically analyze historical data based on the established hose inspection and replacement frequency to determine whether any interval should be shortened or extended for safety or budget reasons. Destructive testing of the replaced hose can determine whether the hose is replaced too early or too late.
Post time: Feb-23-2022